QA / QC
HazTech Solutions work with OEMs (Original Equipment Manufacturers) and End Users to provide project specific QA/QC Verification and Inspection Services. Our team of experts are equipped to ensure compliance of equipment with the relevant standards, codes and regulatory requirements. Our QA/QC services are tailored to suit the needs of our customers and are broken down into the below key areas.
Vendor Inspections
This involved inspecting items at their place of manufacture before delivery. This is the most convenient and cost-effective way to determine whether a product, service, process, piece of equipment or installation complies with site specification, customer expectations, applicable regulations and standards or othe applicable requirements. Our unique approach means we engage with our customers and their teams early ensuring they have the right knowledge, skills and understanding of the relevant codes and standards to ensure they can meet the installation requirements as stipulated by the end user. This approach ensures that through the manufacturing process, costly changes and re-works are limited, expectation is understood and installation teams are equipped with the right amount of knowledge to ensure they can manufacture products that meet specification in a timely manner.
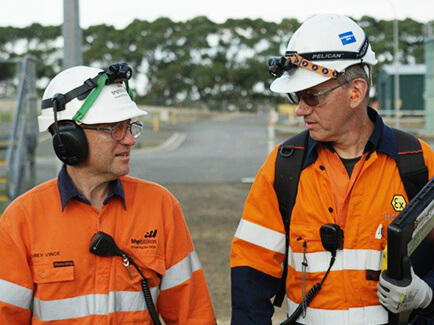
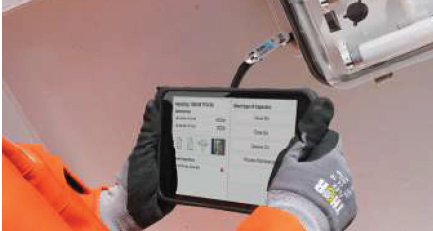
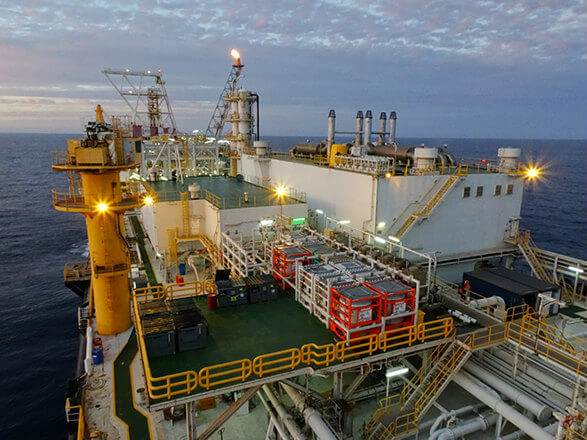
HazTech remain on hand through the lifecycle to assist and advise vendors providing the following support:
- Atex/Compex/EEHA/IECEx Awareness
- Design Verification
- Gland Training
- Installation Techniques
- Simplifying end user requirements
- Periodic Inspection
- Conformity Assessment Documents
- Factory Acceptance Testing
- Declaration of Conformity
- Site Acceptance Testing
- After sales service and support including required construction/modification requirements.